본 글은 국산목재 합판 전용 공장의 중요성을 어필하기 위해 써졌다. 일본은 약 30 년에 걸친 노력 끝에 30여 개의 합판공장이 모두 자국산 삼나무와 히노끼 등의 원목을 100% 사용하는 전환을 이뤘다. 연구와 개발 과정을 거쳐 직경 14cm까지의 소경목을 박심 3.5cm까지 깎는 설비와 기술을 보유했다. 일정한 단판의 품질과 건조 성능, 접착제 등을 혁신한 결과 원목에서 제품까지의 수율이 68%에 이르는 경쟁력 또한 갖췄다. 한국의 합판 설비는 수율 55%에도 미치지 못할 정도로 낡아 우리의 국산재를 이용할 수 없는 현실이다. 탄소중립시대에 부흥하는 국산 원목 생산이 가능한 임지 부근에 국산목재 전용 합판공장이 이제 더 늦기 전에 들어서야 한다.
목재 자급률 15.7%, 내용은 더 빈약, 합판 생산은 제로
2020년 우리나라는 목재제품을 생산하기 위해 투입된 원재료는 842만㎥. 이 중원목은 637만㎥(76%)이고 원목 이외는 205만㎥(24.4%)다. 842만㎥ 원목 중 국산 원목은 366만㎥(43.5%)이고 수입 원목은 271만㎥(32.3%)다. 이 중 313만㎥ (37.2%)가 제재공장에 투입됐다. 제재공장에 투입된 원목 중에서 국산 원목은 55만㎥(17.5%)가 투입됐다. MDF 제조공장은 투입 원목 180만㎥ 중에서 70.7%에 달하는 127만㎥가 국산 원목으로 투입됐다.
이에 비해 합판공장은 연간 28만㎥의 원목 등을 사용했지만 국산 원목 투입량은 0%이다. 50년 이상 산림 경영을 통해 가꿔 생산한 국산 원목 34.7%는 MDF공장으로 15.0%는 제재공장으로 투입됐고, 나머지 약 50%는 연료용 펠릿, 칩 등을 생산하는 공장으로 투입됐다. 우리 땅에 우리 손으로 정성껏 관리한 국산원목 대부분이 다양하게 이용되지 못하고 섬유판공장과 연료와 에너지자원 등으로 편중 공급되고 있다. 반면 수입 대체 효과가 크고 목재제품 중 고부가가치 제품을 만드는 합판공장에는 국산원목 한그루 이용하지 못한 현실이다. 시급히 개선돼야 할 부분이다.
일반적으로 월간 합판 생산량 6천㎥ 규모 합판공장에 투입 원목은 약 1만㎥이다. 국산원목 중 합판용으로 사용 가능한 원목은 낙엽송, 소나무, 잣나무, 편백나무 등이 있다. 2020년 산림청 자원조사통계를 보면 낙엽송 산림면적은 24만ha, 임목 축적량은 ha당 216㎥로 5천2백만㎥ 정도가 강원, 경북, 충북 지역에 분포돼 있다. 이 중 40년 넘은 벌채 가능 낙엽송은 연간 1백만㎥ 이상 이지만, 산림청은 2021년 기준 50만㎥를 벌채했고, 매년 10% 정도를 확대해 2024년에는 70~80만㎥ 벌채하겠다고 한다. 이 중 합판용으로 사용가능한 특용재급이나 1등급재 낙엽송으로 원목경 30cm 이상만 대경목 비율이 강원도 경우 ha당 153본으로 합판용으로 공급에 있어 의지만 있다면 충분히 공급이 가능한 원목량이다. 물론 합판공장에서 원목경 30cm 이상만을 고집해 사용할 수 없다. 국내 산림 환경을 고려하면 합판공장은 원목경 15cm에서 30cm까지의 원목을 합판공장에서 사용해야 한다. 하지만, 우리나라 합판공장 현실은 어떠한가?
국산재를 전량 사용하는 일본의 합판산업
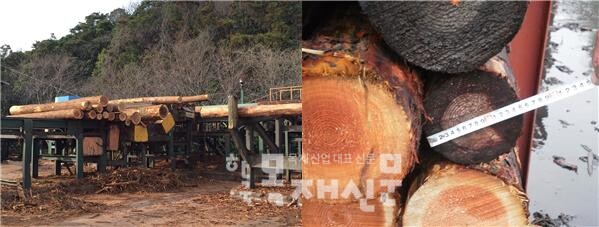
수입 원목처럼 합판용 원목이 원활하고 충분하게 공급되는 것에 반해 국산원목 상황을 고려하면 소경목도 절삭 가능한 제조 설비가 우선돼야 한다. 현재 국내 합판회사 중 선앤엘과 성창기업만이 원목을 절삭할 수 있는 로타리 레이스(Rotary Lathe)를 보유하고 있고, 이건산업은 최근 로타리 레이스와 건조기를 철거하고 전량 수입 베니어로 합판을 만들고 있다. 현재, 합판제조설비 중에서 국산 원목으로 채산성이 맞는 절삭이 가능한 회사는 있는 것일까? 현재 보유한 로타리 레이스로 소경목 절삭이 가능 할까? 라는 의문이 생긴다. 잘라 말하면 국내 합판회사들의 설비로 단판을 깎는 자체는 가능하겠지만 수율 측면에서 보면 전혀 답이 나오지 않는 설비다. 수율은 제품원가에 지대한 영향을 미친다. 대부분 일본 침엽수 전용 합판공장은 공장제품 수율이 68% 이다. 어느 경급(径級)까지 공급해야 제품 수율이 보장될까?
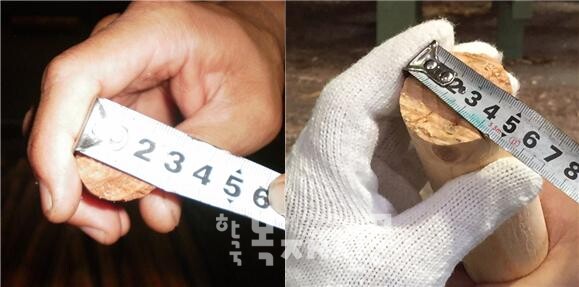
원료 특성은 합판공장에서 중요 요소다. <사진 1>처럼 일본 합판공장 대부분 14cm 이상 소경목을 이용하며, 평균 원목경은 20cm를 넘지 않고 제품 수율을 놀랍게도 68%에 달한다. <사진 2>처럼 심지어 원목 절삭 후 심목경(芯木径)은 3cm~4.5cm까지 절삭 가능한 로타리 레이스로 단판을 깎는다. 합판공장 생산성은 원목을 가공하는 첫 단계인 절삭공정에서 결정된다. 물론 수율을 높이기 위해 30cm 이상 대경목을 사용하면 생산성이 향상되지만 요즘 원목 공급이 열악한 상황에서 대경목을 합판에 이용하기보다 건축재로 이용하는 게 더 나을 것이다. 소경목이지만 다양한 원목경과 수종에 완벽하게 대응 가능한 로타리 레이스 선택이 중요한 요소다. 또한, 원목 상태도 중요하다. 즉, 옹이가 없고 곧바른 원목을 사용하면 당연히 수율이나 작업성이 향상 되지만, 현재 원목 수급 상황을 이해한다면 현실적이지 않다.
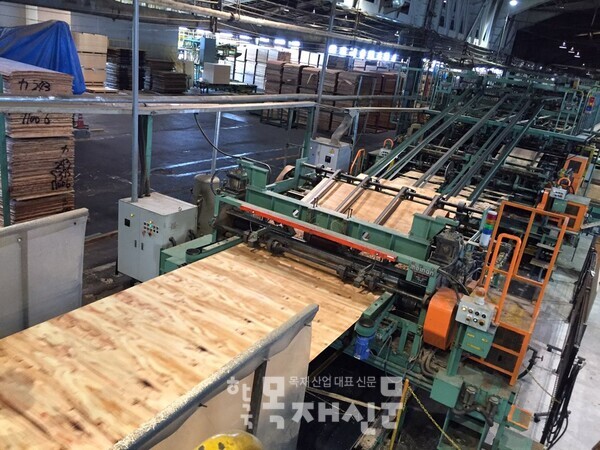
<사진 3>처럼 일본 침엽수 합판공장에서 사용하고 있는 대부분 원목은 삼나무와 편백이다. 삼나무 내부는 옹이가 가득하다. 이러한 원목을 절삭해 구조용 합판과 마루 대판을 생산한다. 1990년대 침엽수 합판 제조 초창기 일본은 옹이가 많은 삼나무와 편백 베니어로 합판 코어로 사용하고 표층(Face)과 후면(Back)은 캐나다산 더글러스 퍼(Douglas Fir)를 사용했다. 합판제조를 위해 약 10% 원목을 캐나다에서 수입했다. 하지만 지금은 이마저도 국산 원목으로 대체해 100%에 가까운 97% 국산재 합판을 만들고 있다. 이는 설비의 혁신적인 개발과 건조 기술, 접착제 성능 향상 등이 융합된 결과이다.
벌채와 이용의 국민 인식 변화
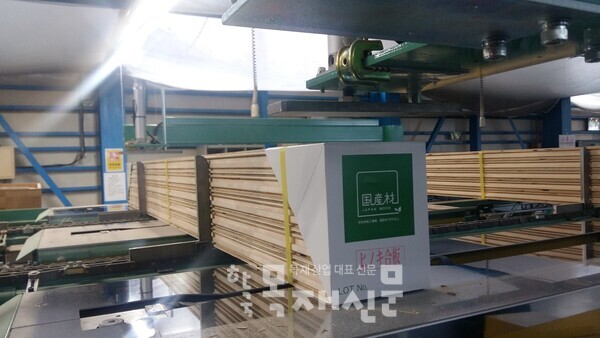
일본은 국산 원목을 100%에 가깝게 사용한 합판 등 각종 목재제품은 국산재(國産材) 인증을 표시해 소비자 선택폭을 넓혀 갔다. 국산 원목을 사용한 제품을 이용한 소비자도 자긍심을 갖도록 했다. 이를 통해 지속가능한 삼림자원에 대한 국민 인식이 변화하고 삼림은 심고 키우고 베고 활용하는 순환시스템에 대한 이해가 넓어지고 깊어진 효과도 있다. 목재를 이용하려면 대부분 국가에서 겪고 있는 나무를 베면 자연 파괴, 환경 훼손이라는 벌채 부정 인식을 바꾸는 게 중요하다. 삼림을 그대로 두어야 그릇된 인식을 지금이라도 바뀌도록 정부 기관와 전문기관의 노력이 필요하다. 이를 위해 정부의 강력한 지원과 국산재를 사용해 제품을 만들고자 하는 회사나 개인에게 폭넓은 인센티브를 제공해야 한다. 일본 마루 포장 측면에 국산재 표시를 해 제품을 사용하는 소비자가 바로 국산재를 활용한 제품이라는 것을 알리는 홍보 효과를 불러일으키고 제조사와 소비자 사이의 신뢰를 심어주는 것을 참고할 필요가 있다<사진 4>.