탄화보드 제조 후 기능성 및 고강성(高剛性)을 지닌 다른 재료를 부착 또는 코팅하여 미관을 개선할 수 있다. 섬유판을 미리 타공(打孔)한 후 탄화하거나 샌드블라스팅(sand blasting) 기법을 적용하여 탄화보드의 표면에 음양각(陰陽刻)을 실시하여 작품화할 수 있다(특허 101164626. 그림 6).
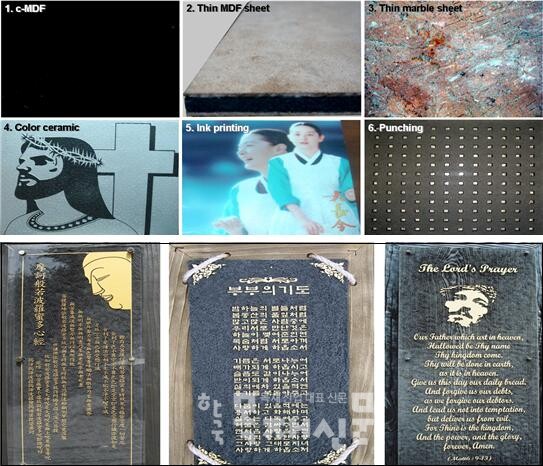
밋밋한 섬유판에 목리가 선명한 무늬목(예: 물푸레나무)을 입힌 후 탄화하면 원목의 질감을 탄화보드에 생생하게 부여할 수 있다. 한편 1차 저온 탄화한 무늬목 탄화보드에 수지를 함침한 다음 다시 고온에서 탄화하면 고밀도 탄화보드의 제조가 가능하다(특허 101374599. 그림 7). 그 외에도 필자가 근무했던 국립산림과학원은 탄화보드와 관련하여 다수의 특허를 보유하고 있다.
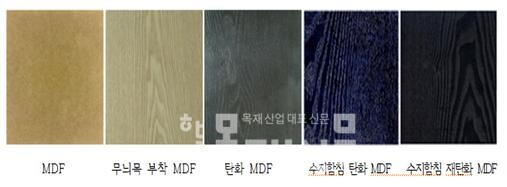
다양한 온도(400~1,000℃)에서 제조한 MDF 탄화보드의 성능을 평가한 결과, 폼알데하이드, 톨루엔, 라돈 흡착, 조습성 및 전자파차폐효력이 매우 우수하였다. 또한 화재 시 불에 잘 타지 않고 유독가스 발생이 없었다. 2021년에는 흡착된 각종 유해 VOC를 자체적으로 분해할 수 있는 “가시광 응답형 광촉매 탄화보드 제조 방법”에 대한 특허가 국립산림과학원(이민 박사), 전북대(문성필 교수) 및 필자 공동으로 등록되었다(특허 10-2221738).
현재 탄화보드는 1개 공장에서 소규모로 주문 생산되고 있으며, 편백이나 자작나무 벽판재(일명, 루바)의 뒷면에 얇은 탄화보드(3,7T , 6T)를 삽입하는 형태로 제작되어 “차콜우드보드”의 상품명으로 복지회관이나 전원주택의 벽이나 천장, 드레스룸용 내장재로 활용되고 있다. 금후 탄화보드에 대한 사회적 수요가 증대하고 경제적을 갖춘 대량생산 시스템이 구축된다면 탄화보드는 친환경 건축자재로서 주거환경 개선에 크게 기여할 것이다.
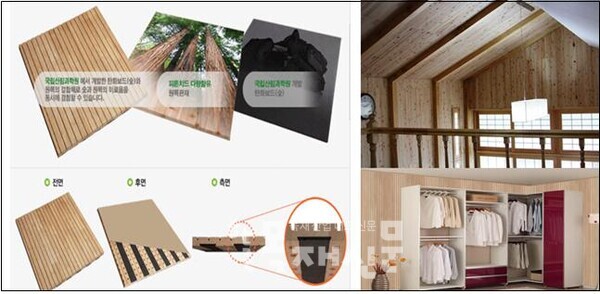
3. Charcoal porcelain
우드 카본을 제조하는 방법으로 3번째로 소개할 제품은 숯 자기이다. 숯은 나무를 탄화하여 만든 것이고, 자기(瓷器)는 백토(白土) 따위로 구워 만든 사기그릇으로 흡수성이 없어 식기나 장식품으로 쓰인다. 즉 숯 자기란 목탄을 자기처럼 만든 것이다.
일상생활에서 다양한 제품으로 사용할 수 있도록 제조하는 “원목을 이용한 숯 자기의 제조 방법”에 대해서는 특허(등록번호 10-0835249, 발명자 장종한)를 통해 간단히 소개한다. 다양한 원목 가공품을 원목 그대로 보존하면서 수분을 제거한 후 구워내어 숯의 효능을 그대로 제공할 수 있다. 진공상태에서 나무로부터 우드세라믹 탄화물을 만드는 새로운 기술이다.
종래 원목으로 이루어지는 가공품은 목기, 제기, 쌀뒤주 등 다양한 제품이 제안되고 있으나 이를 숯으로 변환하여 사용하려면 원목으로 가공된 가공품이 숯으로 변환되는 과정에서 뒤틀리거나 갈라지는 다양한 변형에 의해 사용이 불가능한 제품으로 변하게 된다. 또한, 변형된 제품을 재가공하여 사용할 수 없다. 원목 가공품이 숯으로 변환된다고 하더라도 강도가 약하므로 일상 생활용품으로 사용할 수 없는 결점을 갖게 된다.
원목 가공품은 느티나무, 물푸레나무, 사방오리나무(야사부시, ヤシャブシ), 은행나무 등 다양한 나무를 이용하여 자연 건조한 후 원목을 회전시키면서 칼날을 이용하여 목기나 제기 등 다양한 물품을 가공한 후 건조시켜 옻칠을 통하여 사용되도록 하였으나, 원목 가공품을 원형 그대로 보존한 숯으로 제공한 예는 없었다.
숯으로 만든 제품을 그릇에서 각종 모양의 잔, 유골함, 도마, 등기구 등 다양하게 사용하기 위해서는 일정한 강도를 제공해야 하지만 수분을 제거한 제품은 외부의 충격에 약하므로 제품으로서의 강도를 제공할 수 없는 것이었고, 제품으로 사용할 수 있는 강도를 제공하기 위해서는 인공적인 접착제 등과 같은 물질과 혼합하여 사용하게 되므로 숯 고유의 특성을 제공하지 못하는 결점이 있었다.
이러한 종래의 결점을 해소시키기 위하여 자연 건조된 원목을 이용하여 다양한 제품의 형태를 갖도록 가공한 후 가공한 원형 그대로 보존한 숯 자기로 제조한다. 이 발명은 원목을 이용하여 다양한 제품의 형태로 가공한 후 원형 그대로 보존한 숯 자기로 제조하여 일상생활에서 사용 가능하도록 강도를 부여함을 목적으로 하는 것이다. 숯 자기로 제조한 다양한 제품을 제공하여 숯의 기능인 원적외선 방사기능, 음이온 방출기능, 부패방지 및 탈취기능 등의 작용을 통해 보관물의 냄새를 탈취함은 물론, 유해 중금속을 흡착 제거하여 보다 안전하고 맛이 그대로 유지되도록 함을 목적으로 하는 것이다.
상기 특허에 따른 숯 자기의 제조 순서는 다음과 같다.
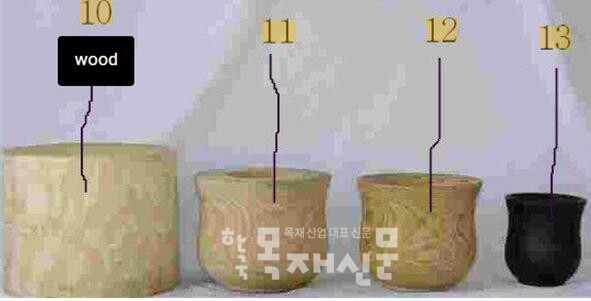
① 채취한 원목(10)은 자연 건조한 상태에서 30∼90%의 수분을 함유하고 있게 되므로, 건조기에 넣어 30∼150℃의 온도에서 1주일간 건조하여 5∼8%의 수분이 함유되도록 건조한다(원목 건조 단계).
② 건조한 원목을 실제 제품과 동일한 형상으로 1차 가공하여 가공품(11)을 성형하되, 실제 제품보다 체적이 35∼60% 정도 더 크게 가공한다(제품 가공 단계)
③ 가공품을 건조기에 넣어 진공상태에서 120∼180℃의 온도로 15∼30시간 동안 건조하여 숯으로 가공한다(숯 가공 단계)
④ 숯으로 가공한 다음 끓는 물에 넣어 30분 정도 삶아 소독을 한다(소독 단계)
⑤ 숯을 말린 다음 5∼10회의 옻칠을 수행하여 전체 면에 골고루 옻칠이 이루어지도록 한다(옻칠 단계)
⑥ 숯 자기(13)의 표면에 자개를 붙이거나 그림을 그려 넣은 후 100℃에서 2∼25초간 열처리하여 투명 옻칠을 한다(채화 단계)
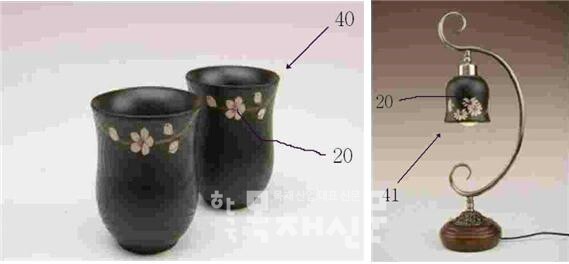