섬유판 ④
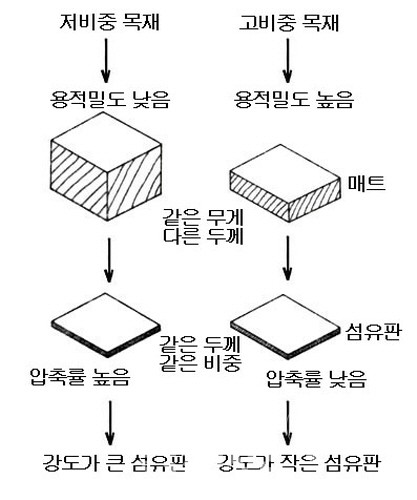
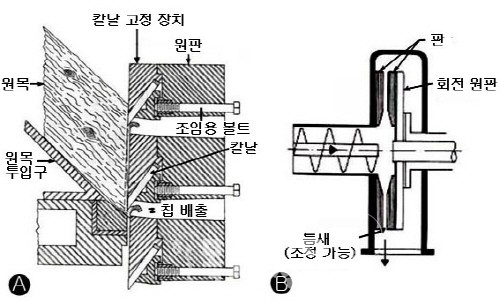
중밀도섬유판은 오늘날 대개 건식법에 의해 제조되고 있는데 그 공정의 첫 단계는 경질섬유판 제조 공정과 비슷하다. 원목뿐만 아니라 합판 및 가구 폐잔재 또는 제재목 토막과 같은 여러 원료들로부터 먼저 칩을 생산한다. 그후 칩은 열기계펄프 경우처럼 정쇄된다. 왁스(wax)는 대개 해섬 공정중에 첨가된다. 그 다음 공정은 삭편판 제조 공정과 매우 비슷하다. 중밀도섬유판인 경우 큰 부피를 지니는 낮은 밀도의 섬유를 사용하기 때문에 특수한 접착제 혼합 장치와 성형 장치가 필요하다. 대부분의 중밀도섬유판 제조 공정에 있어 접착제는 정쇄기와 건조기 사이의 송풍관에서 혼합된다. 이 경우 접착제는 가속 송풍관 내부로 주입되어 바람에 의해 빠르게 움직이는 정쇄된 섬유를 때리게 되고 그후 관 내부에서 격렬하게 요동치는 섬유에 의해 더욱 혼합된다. 요소수지는 대개 전건무게 기준으로 8~12% 정도의 함지율이 되도록 첨가된다.
일부 특수 제품인 경우 함지율을 15% 이상으로 높여주게 된다. 그후 접착제가 도부된 섬유는 플래시튜브건조기에서 고온으로 건조된다. 섬유의 건조를 통해 열압 시간을 단축할 수 있으며 파열에 따른 박리 현상을 줄여 줄 수 있다. 건조기를 통과하는 시간은 요소수지접착제가 경화되지 않을 정도인 10~29초 정도 수준으로 설정해 준다. 마지막으로 매트로 성형되고 열압을 통해 최종 제품으로 제조된다. 다양한 종류의 원료가 중밀도섬유판 제조용으로 사용될 수 있다. 자동대패에 의한 세이빙, 톱밥 및 합판 조각과 같은 폐잔재가 대개 사용되고 있으나 바람직한 품질의 원료를 얻기 위해서는 펄프용 칩을 적어도 25% 정도 섞어 주어야 한다. 농산물 섬유 자원은 중밀도섬유판 제조용 원료로 상당한 잠재력을 지니는데 현재 여러 공장에서 이들을 사용한 제품이 생산되고 있다. 예를 들면, 야자수 줄기가 중밀도섬유판 원료로 말레이시아 및 인도네시아에서 널리 사용되고 있다.
원료 섬유와 접착제 사이의 화학적인 상호 결합이 적절하게 이루어지는 경우 다양한 섬유 자원들을 사용할 수가 있다.
① 원료
섬유판의 원료로써는 당분을 짜고 남은 사탕수수 찌꺼기나 곡물 짚 등도 사용될 수가 있으나 목재가 가장 많이 사용되고 있다. 삼나무, 편백, 소나무, 너도밤나무, 피나무 등 침엽수재나 활엽수재에 관계없이 가격만 저렴한 목재라면 어떠한 것이라도 모두 원료로 사용할 수가 있다. 압체시 세포벽이 얇기 때문에 섬유의 찌그러짐이 쉽게 발생함으로써 섬유간의 접촉 면적이 커지고 결국 섬유간의 강한 결합이 가능한 저비중의 목재가 더 바람직한데 고비중의 목재는 열압시 압축률이 낮아 섬유간의 밀접한 접촉을 기대하기 어렵기 때문에 적당한 원료가 되지 못한다(그림 1).
이외에도 합판 공장 등으로부터 배출되는 박심목(剝心木, core)이나 폐잔재, 목질계 건축 폐기물, 야자열매 껍질 섬유 등 역시 원료가 될 수 있다.
② 조목
섬유판용 펄프는 대개 목재칩으로부터 생산되기 때문에 먼저 원목을 원판형 칩 제조기(disc chipper) 등을 이용하여 적절한 형상의 칩으로 절삭하여야 한다(그림 2). 칩에 수피가 15~20% 정도 혼입되어 있어도 섬유판의 강도에는 큰 문제점이 되지 않으나 담색의 섬유판 제조와 같이 특정 제품을 목적으로 하는 경우에는 수피가 얼룩 반점으로 나타날 수 있기 때문에 완전히 박피를 한 다음 칩을 제조하는 것이 바람직하다. 그러나 미송이나 폰데로사소나무 등의 수피에는 왁스(wax) 성분이 존재하기 때문에 사이즈제(size)로써의 역할을 나타내게 되어 흡수율 개선에 도움이 된다.
<다음호에 계속됩니다.>
국민대학교 임산생명공학과 엄영근 교수